Exciting Developments at 737DIYSIM: Behind the Scenes
- May 23
- 5 min read
Updated: Jun 3
The Journey So Far
Hello Everyone,
It's time for a blog post to explain what's going on behind the scenes here at 737DIYSIM. The poor old website has been neglected since January, and you wouldn’t believe the number of emails we get just asking if the website is still going! Yes, it is, and it is supported by me, Karl, and my wife, Helen.
Helen runs the website, emails, and AI, which is still a work in progress. You may have seen the AI window on the site. This curious feature has brought us many funny comments. My phone alerts me when AI answers on my behalf. Should it provide incorrect information, we step in to correct it. Nonetheless, it's a fantastic tool that has cut our workload by 50%. Questions like, "Where can I find the wiring video?" or "Where can I find the build guide?" are now easily addressed. The AI links directly to these pages, saving us from constant replies.

Embracing AI in Our Workflow
Some of you don’t enjoy AI; we can tell by the comments we receive: "Please die!" "Go away and turn off," etc. This does make me smile. I understand the concerns, but as a tool that can answer common questions, it is a phenomenal resource. I hope it will reduce the number of emails we receive.
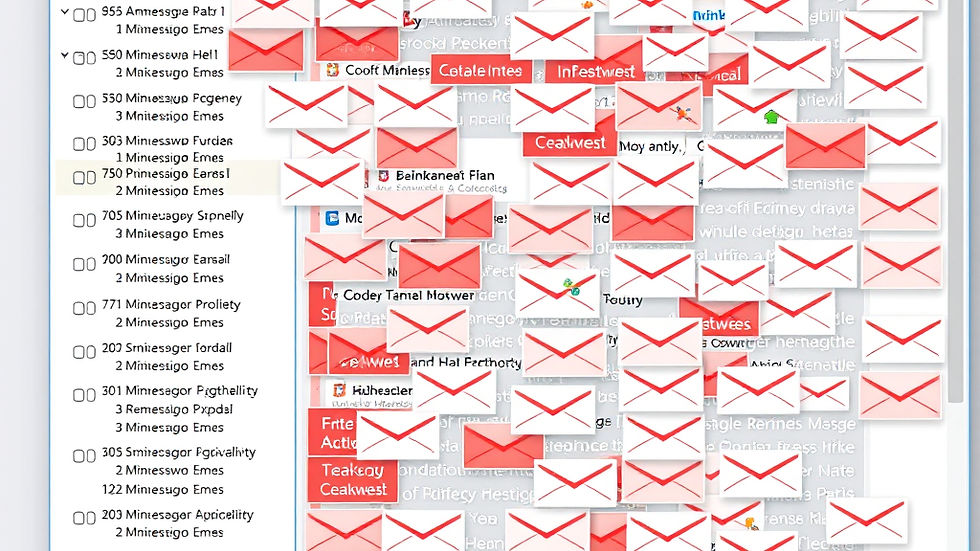
Speaking of emails, it’s just the two of us on our team. Helen and I have been relying less on our children, who have reached their teenage years and are almost independent. Helen can manage about 200 emails daily in an 8-hour workday. Unfortunately, we often receive double that on a slow day. Each email takes time to locate the necessary link on the website and respond, leading to even more follow-up emails. So we appreciate your patience!
737SS: A Flight Simulator Revolution
As for me, ever since we attended the FSweekend Flight Sim Expo, the 737SS (Single Seat) has taken off for DIY sim builders. Our techniques and design have reached new heights, enhanced by our new complementary PCBs for each design. After completing the MIP, we found 3D printing to be a viable and affordable solution.
The support and requests to push this project further at the expo have exceeded our wildest dreams. We started with the 3D printed window structures, which were a challenge to reproduce in wood. Many have tried but failed. They are among the most complex shapes to get right with all their intricate angles. We printed the expo pieces in Bambu PLA-CF, which hides the layer lines and mimics real aircraft trim. This was the catalyst for advancing our 3D printing.

The Prototype internal structure of the 3D-printed 737 shell still needs to be smoothed, filled, and painted for a perfect finish.
Next on our agenda was the 3D printed sidewall, complete with glorious shapes and details. Yesterday, we finished the front window matrix. Our current task is to produce the working overhead structure.
The Facts Behind the Build
Let’s discuss some facts, as I know many people have doubts. This project isn’t for everyone. It’s for those who may lack the skills and want the printer to do the work. As of this morning, the entire shell has consumed 21 rolls of filament, totalling nearly £300 at £14 a roll from Bambu. The windows alone weigh in at 7.13 kg.
The overhead v1 structure took 49 hours to print, using two printers. Meanwhile, the sidewall consists of 52 parts, averaging 2 hours and 13 minutes each for printing. I'm sharing these details to prepare you for what to expect. Decide if this might be a good fit for you or if it’s not quite right.
After successfully printing the Windows prototype for the expo, I've realized this is a viable option with modern print speeds and quality.

For those of you who are more experienced builders, whole sections of the shell can be replaced with wood. This could lead to a stronger unit and a quicker build. Nevertheless, the added detailing from the print enhances the final appearance.
A Work in Progress
This is still a massive project in progress, and I wanted to explain where I have been for the last five months. Constructing the shell from plastic, similar to the real aircraft with its frames and stringers, has been a labor of love!

It's such an exciting journey! Significant steps forward have been made this week. I managed to move on to the front window assembly. The sidewall and side windows are now complete and printed up to the top of the window frames. However, the top part requires adaptation to work with the overhead structure.
The front window and new glarewing have turned out spectacular! The glarewing now features the slanted side, with chrono and mic buttons fitted. This design was complex but worth the effort. If you're ever going to build one, I can't recommend Bambu PLA-CF enough for an incredible layer line-free finish.

Design Considerations
I hope you can see how much design work has gone into this journey. Each part is assessed for ease of build and structural integrity. Unfortunately, I cannot share the designs yet, as they all need adjusting once assembled. I've focused on perfecting the shapes, ensuring that they all fit together correctly.
For instance, with the sidewall, I need to create new parts to include features such as the tiller, doc holder, and oxygen mask. The side windows also need some adjustments. However, no releases can happen until the front and overhead structure interfaces are completed.

Smiling at the very first prototype. This window complex doesn't yet have the curved external surface.
This is an epic journey that I can’t wait to share with you all, and I look forward to seeing your versions of my work appear online. We are still here and working hard on my passion. A massive thank you to all my Patreons for their support. Without them, the prototyping and printing to refine parts would never have been possible.
That’s enough waffling for now; it's time for me to get back to designing more parts!
Kind Regards,
Karl
What a great accomplishment, it is so great to see what you are building. Would it be possible to build a full cockpit with 3D printing that would be so awesome.